The aviation and aerospace industry is one of the most highly regulated sectors globally. As the industry evolves, the need for robust supply chain management continues to grow. Amidst the complexities of global networks and the pressing demand for sustainability and safety, companies must turn to innovative and secure traceability solutions that can uphold increasingly stringent industry standards and compliance, and combat the growing problems around safety and sustainability.
One of the most promising solutions to these challenges is the Digital Product Passport (DPP).
By establishing cradle-to-grave or end-to-end traceability within the aviation and aerospace industry supply, chains, the DPP extends beyond mere compliance and represents a strategic shift towards transparency and accountability. This article delves into how DPPs can help ensure compliance with industry standards and regulations, improve lifecycle management, streamline aircraft component tracking, prevent counterfeit parts, improve the disposal of end-of-life aircraft, and support the production and use of sustainable aviation fuel (SAF).
The emergence of digital product passports (DPPs)
Digital product passports are electronic records that contain detailed information about a product, from its creation to its final disposal. These records serve as a secure, traceable, and easily accessible source of information for manufacturers, suppliers, regulators, and end-users. By providing a comprehensive record of a product's history, DPPs facilitate transparency, efficient sharing of relevant information, and collaboration among stakeholders. This ultimately improves safety, reliability, and environmental sustainability.
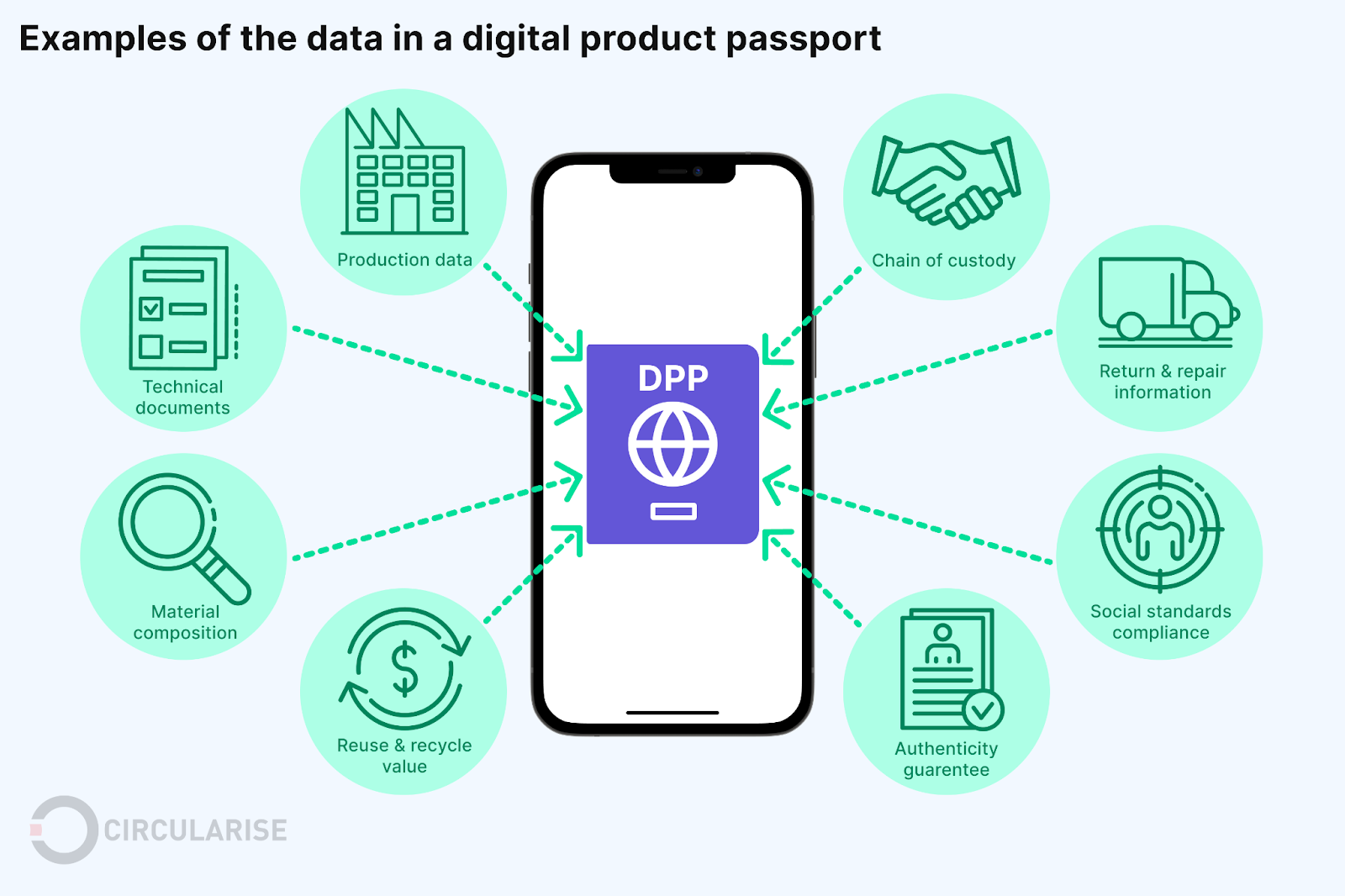
The mandatory introduction of the battery passport by February 2027 represents a significant step forward for environmental and consumer protection. With the European Union leading the charge, this initiative mandates that all electric vehicles (EV) and industrial batteries over 2 kWh sold within the EU market must have a unique DPP. This passport will provide vital data on the battery's lifecycle, from its carbon footprint to the recycling efficiency of its materials1 – all accessible via a QR code.
In the aviation and aerospace industry, the integration of DPPs could mirror the stringent standards set by the EU's battery passport initiative. By adopting similar digital tracking mechanisms, the industry can ensure that each aircraft component, from the smallest bolt to the most complex engine part, adheres to the standards of safety, sustainability, and compliance.
How DPPs enhance traceability and compliance
The aviation and aerospace sectors are governed by an intricate web of regulations that form the backbone of industry standards, ensuring consistency, and safety, all while requiring global cooperation.
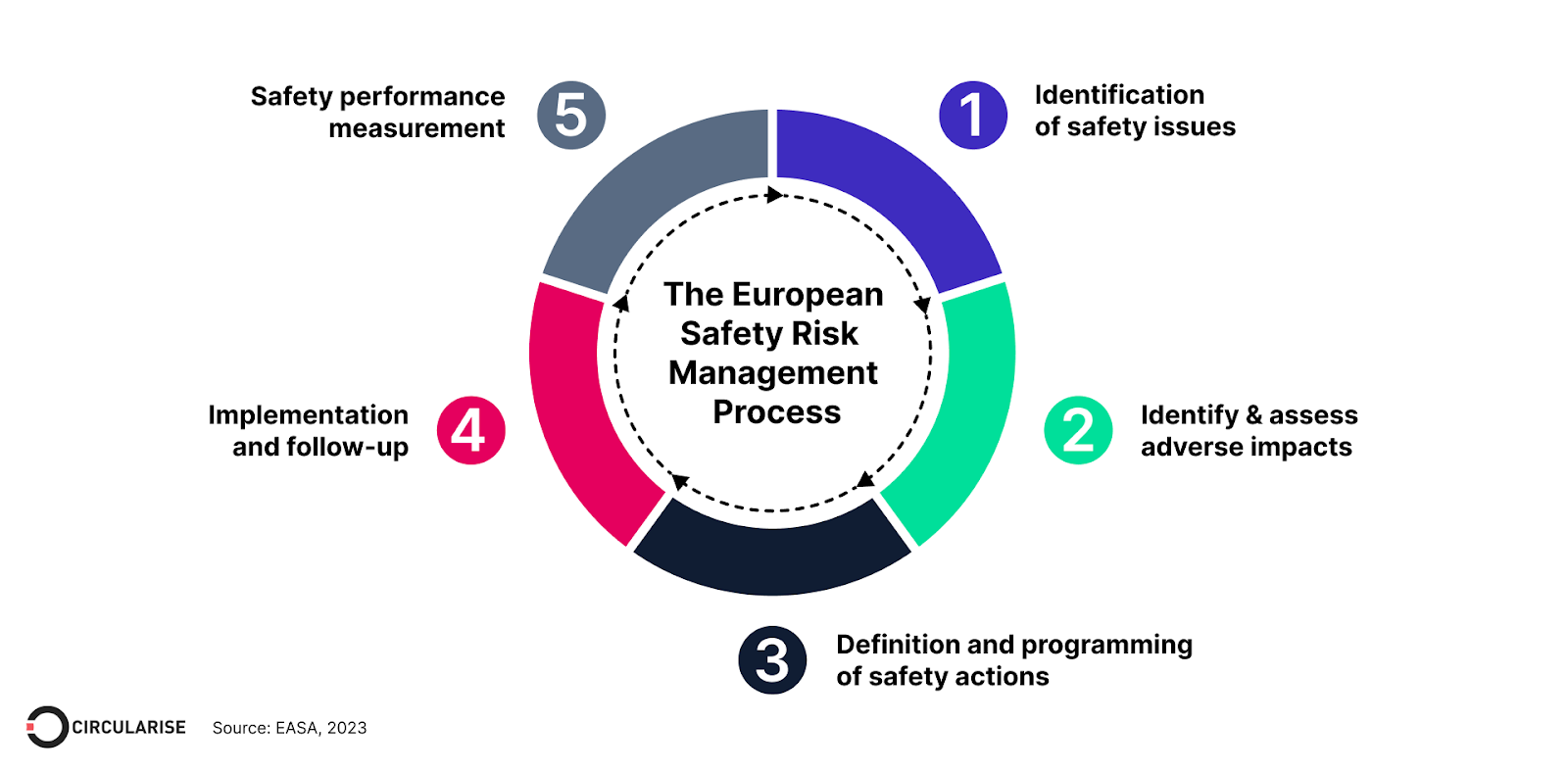
To meet these rigorous standards, supply chain traceability is necessary for companies to monitor and verify compliance with standards and regulations, such as those set by the Federal Aviation Administration (FAA), the European Union Aviation Safety Agency (EASA), and the International Organisation for Standardisation (ISO).
Read more about the specific regulations and standards in aviation that would benefit from traceability solutions.
Aircraft component tracking and certifications
The aviation industry's certification of airworthiness relies on a system of accurate documentation and traceability. However, tracking and managing the lifecycle of aircraft components is a complex and time-consuming process that requires coordination among various stakeholders, including manufacturers, suppliers, maintenance providers, and regulators. While supply chain traceability is essential for industry players to comply with maintenance regulations and uphold quality standards, the mandatory documentation that accompanies aircraft parts during a commercial transaction requires more specific regulatory direction.
The FAA and EASA, along with various quality assurance programs, have established guidelines to maintain these standards. However, they are not legally binding but rather, serve as recommendations. Current documentation tracks crucial information such as flight hours, cycles flown, and the remaining life of aircraft parts, yet these regulations lack standardisation and more detailed requirements. This gap leads to confusion, burdensome paperwork, and an increased risk of counterfeit parts entering the system.
The perils of counterfeit parts in the aviation industry
Despite the stringent regulations, the aviation and aerospace industry is still susceptible to the infiltration of counterfeit parts. The Federal Aviation Administration (FAA) estimates that approximately 520,000 counterfeit or unapproved parts make their way into planes each year.2 While this figure may represent a small fraction of the millions of components in use, the impact of even a single failure can be devastating.
The alarming discoveries of counterfeit parts in Boeing aircraft and subsequent investigations by aviation giants such as GE and Safran3 highlight the extent to which counterfeit components can penetrate even the most regulated and safety-conscious environments.
Counterfeit parts range from minor components to critical engine pieces, each carrying the risk of failure due to substandard materials, improper manufacturing, and untested performance. These unauthorised components, often indistinguishable from genuine articles, are a deadly threat to the safety and integrity of aircraft operations.
Aviation regulations primarily focus on restoring aircraft to airworthy conditions through the installation of certified parts, the commercial sale of these parts is subject to a different set of regulatory obligations, quality considerations, and economic factors. The presence of counterfeit parts within Boeing's supply chain also underscores a broader systemic problem: the challenges of ensuring the authenticity of parts in a complex and global network of suppliers and distributors.
In response to these incidents, regulatory bodies and industry leaders are calling for enhanced traceability and verification processes. By implementing more stringent checks and balances, The industry can safeguard the aviation and aerospace supply chain against the dangers of counterfeit components by keeping a secure ledger on Digital Product Passports (DPPs). As DPPs provide detailed electronic records of a product's history from manufacture to disposal, it can be an effective tool in ensuring the authenticity and traceability of aviation parts.
Read about how the plastics industry is using traceability to tackle counterfeits.
Sustainable management of end-of-life aircraft
The Global Fleet and MRO Market Forecast for 2024-2034 projects a significant expansion in the global aircraft fleet over the next decade. The Oliver Wyman’s report predicts that the worldwide commercial aviation fleet will expand by 33% to over 36,000 aircraft over the next decade.4
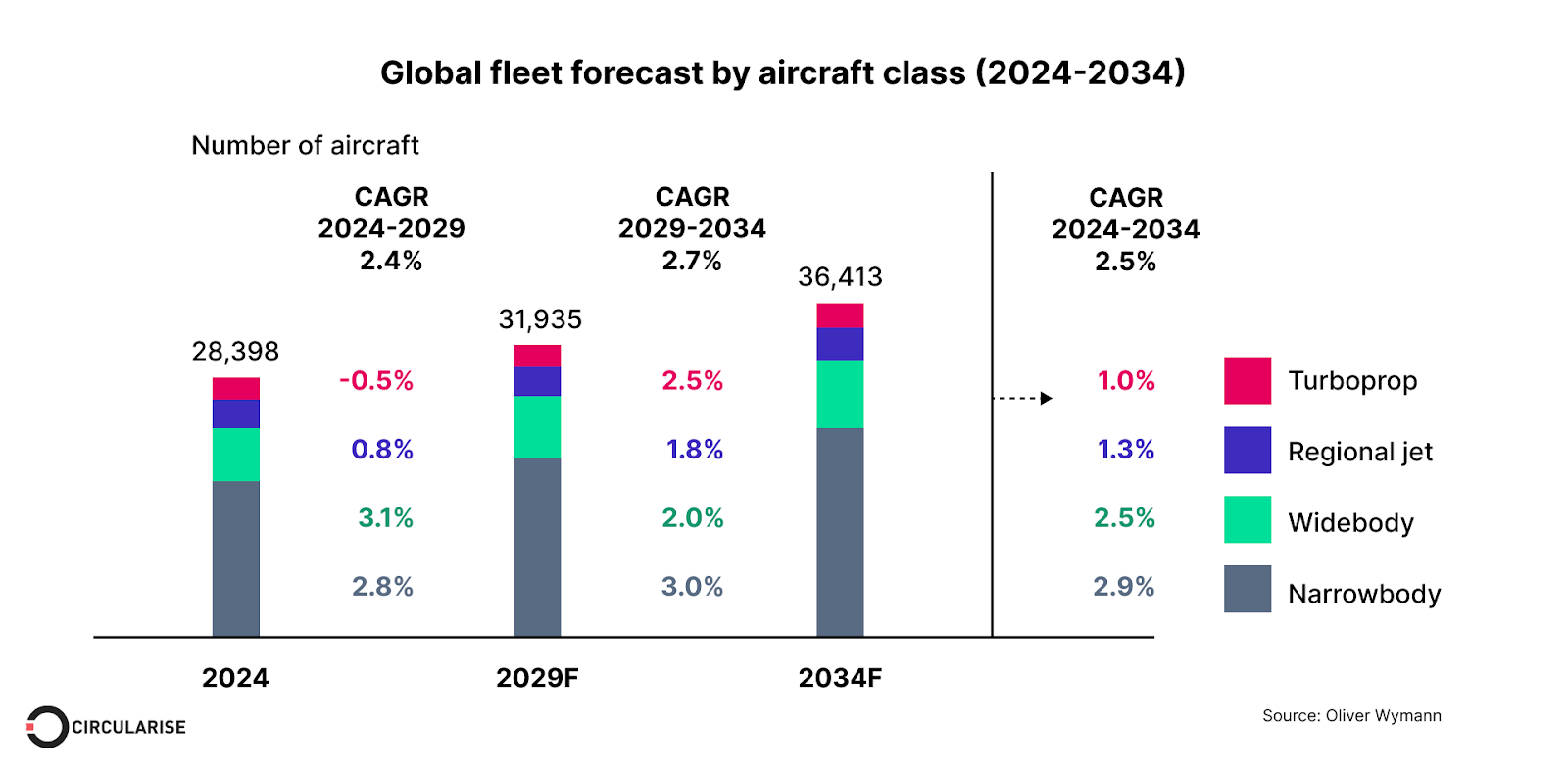
With expanding fleets, the aviation industry is facing a growing problem with the disposal of end-of-life (EoL) aircraft, particularly when it comes to composite materials like carbon fibre and fibreglass. These composites are prized for their strength and lightweight properties, but they also present significant hurdles in waste management and recycling due to their durability and complex material compositions.
Aircraft boneyards are where retired aircraft await dismantling, with composite materials posing a specific issue due to their long decomposition times and potential to release toxic substances into the environment. The Aerospace Fleet Recycling Association (AFRA) estimates that around 15,000 aircraft will be decommissioned over the next two decades, a substantial portion of which will be composed of these problematic materials.
Digital Product Passports (DPPs) that trace an aircraft’s lifecycle from manufacture to disposal ensure that critical information about material composition is not lost over time. This level of traceability is essential for end-of-life management, as it allows for the identification of recyclable components and the safe disposal of hazardous materials.
DPPs can significantly aid in the proper handling of composite waste by providing detailed information that is vital for recycling efforts. It helps recyclers determine the most suitable recycling or repurposing methods for composite materials. Moreover, DPPs can ensure that the valuable materials contained within composites are recovered and reused, contributing to a circular economy and reducing the reliance on finite resources.
Sustainable aviation fuels (SAF) with digital product passports
The aviation industry's quest for sustainability has led to the development and adoption of sustainable aviation fuels (SAF). These alternative fuels are derived from renewable resources and are designed to reduce the carbon footprint of air travel and the reduction of greenhouse gas emissions.
The International Air Transport Association (IATA) forecasts that SAF could potentially deliver up to 65% of the emission reductions needed for the aviation industry to achieve its goal of net-zero CO2 emissions by 2050.5 To fulfil this demand, a substantial increase in SAF production will be essential. The most significant growth in production is anticipated during the 2030s, driven by widespread policy support, the cost-competitiveness of SAF with traditional kerosene, and a diminishing availability of reliable carbon offsets.
However, the integration of SAF into the aviation supply chain adds a layer of complexity, necessitating traceability of fuel origin, production methods, and usage, as well as third-party audits. By incorporating mass balancing data into DPPs, stakeholders can track the sustainable fuel's journey from production to consumption, ensuring responsible sourcing and adherence to relevant regulations.
Every batch of sustainable fuel would have a secure and traceable digital record, incorporating essential data such as the feedstock source, production site, carbon emissions, and third-party certifications. DPPs ensure that all stakeholders—from fuel producers to airline operators—have access to reliable information. This level of traceability is crucial for verifying the sustainability credentials of aviation fuels, facilitating compliance with environmental regulations, and enabling airlines to make informed procurement decisions.
Airbus and Circularise DPP collaboration
Circularise and Airbus have pioneered a Digital Product Passport (DPP) framework for aviation cabin components along with industry partners. This initiative culminated in a successful Proof of Concept, demonstrating a shared commitment to circularity and the potential to revolutionise the lifecycle management of aircraft interiors.
By integrating DPPs, the project paves the way for comprehensive traceability, from procuring raw materials to the end-of-life recycling or repurposing of cabin parts. This ensures that the environmental footprint of aviation waste is minimised, supporting the industry's goal of achieving a fully circular economy. The Airbus A350-1000 cabin project is a testament to the effectiveness of digital technologies in enhancing recycling rates and reducing waste.
The foresight and innovation displayed by Airbus, along with their partners, highlights their proactive approach to sustainability. The successful implementation of this DPP framework sets a new benchmark for the aviation and aerospace sector, reinforcing the importance of collaboration and technological advancement in driving environmental stewardship within aviation.
Conclusion
The aviation and aerospace industry's commitment towards sustainability and safety is evident in its strategies and adoption of initiatives such as the Carbon Offsetting and Reduction Scheme for International Aviation (CORSIA). Their commitment to sustainable aviation fuels (SAFs), energy-efficient aircraft design, and renewable energy use in operations signifies a transformative era for the sector, complemented by robust waste management, recycling, and increasingly transparent reporting practices.
However, the Boeing scandal has significantly eroded consumer trust, casting a shadow over the industry's reputation for safety. With 171 aircraft grounded in the United States alone, the sector is experiencing substantial financial strain associated with the need for additional hangar space and parking for temporary storage of idle planes, as well as increased maintenance and inspections by the FAA.6 Boeing’s sales and stock prices have plummeted, emphasising the huge financial and legal risks of not incorporating reliable traceability solutions into the supply chain.
Although the aerospace sector is not currently the primary focus of current sustainability regulations, early adoption of Digital Product Passports (DPP) can offer significant advantages. Disruptions can be prevented and consumer confidence restored by forward-thinking companies who take the first steps towards greater supply chain visibility. In this way, they can anticipate and adapt to potential future regulatory shifts and position themselves as resilient and responsible leaders in a competitive landscape. But more tellingly, it affirms their commitment to sustainability and safety instilling confidence in consumers and stakeholders alike.
Circularise is the leading software platform that provides end-to-end traceability for complex industrial supply chains. We offer two traceability solutions: MassBalancer to automate mass balance bookkeeping and Digital Product Passports for end-to-end batch traceability.
Let Circularise help you integrate digital product passports and navigate the evolving sustainability landscape of the aviation industry.