The mass balance approach is a chain of custody model which provides the potential for businesses in the chemicals and plastics industry to incrementally transition to using sustainable feedstocks, without the need to set up separate production lines for sustainable products. Mass balancing is guaranteed by third party certification, creating the need for bookkeeping and reporting throughout the supply chain.
Unfortunately bookkeeping and reporting can create a significant administrative burden, which can limit the scalability of mass balancing within businesses. In this article we explore the practicalities of implementing mass balancing which allows verifiable sustainability claims to be made for products with complex sourcing history.
In this article you will learn:
- Why mass balance approach?
- What is a mass balance chain of custody?
- How does mass balance characteristic allocation work?
- How does mass balance work across sites and organisations?
- How can mass balance material allocation be guaranteed?
- Mass balance certification schemes
- Mass balance reporting example
- Challenges of setting up a mass balance system
- The benefits of mass balance
- Where to start with implementing a mass balance approach?
Mass balance: why, what, and how?
Why mass balance approach?
To realise the idea of a circular economy, we must develop ways to circulate all types of resources and energy. Regulations play a significant role in this, for example, the Renewable Energy Directive (RED II)1 and the EU Packaging Levy2 are creating clear goals and incentives to transition to renewable energy and sustainable material use systems.
RED II has set milestones to reach 32% overall renewable energy usage in the EU by 2030 and from 1st January 2021, all EU member states have to pay a levy of €0.80/kg of non-recycled plastic packaging waste. These fees are now being passed on to the private sector, in various ways decided upon by EU member states. However, regulations alone are not enough to drive the sustainable transition.
In the plastics, chemicals, and fuels industries, the transition to sustainable systems requires a significant shift in technologies, product design, and supply chain operations. Currently, the industry is in an intermediary period, where there are various types of recycled, bio-based, and virgin products flowing through systems at the same time. This mixing of various material sources makes it hard to track the quantity and impact of sustainable resources entering and leaving each facility. There are also other risks - human error in record keeping can lead to double counting of sustainability credits, thus making companies appear more sustainable than they really are, and inadvertently greenwashing.
The challenge lies in understanding where different materials are used for production and where they end up. In some cases, this requires the segregation of sustainable and virgin materials, however, it is not feasible in many chemical processes. It would require setting up a duplicate production line, using more resources and energy, which is the opposite of what we want to achieve.
Some chemical processes make it impossible to track the identity of each compound due to their complexity and the nature of their continuous throughput. Therefore if the feedstock cannot be completely switched in one go and segregation of feedstocks is not possible, another tracking approach must be used to maintain a reliable record of the chain of custody of material - the mass balance approach.
RED II identified the mass balance approach as the most feasible way of ensuring sustainable biofuel production. Therefore in order to comply with the regulation for biofuels in the EU, the mass balance system must be used to maintain a record of the chain of custody, material composition, and greenhouse gas emissions of biofuels produced. Other industries such as biomass, food, and textiles are implementing mass balance as well.
What is a mass balance chain of custody?
Mass balance is a chain of custody approach that allows tracking the net amount of sustainable materials as they move through a system or supply chain and ensures an appropriate allocation of these materials to the finished goods based on auditable bookkeeping.3
Mass balancing allows for sustainable and non-sustainable materials to be mixed in an industrial process, but the mass of the inputs and outputs of the system are recorded while also considering the process efficiency (the conversion factor). This ensures that a process is not producing more sustainable products than are possible given the amount of sustainable material feedstock.4
As the net movement of material is the focus of the mass balance approach, it allows for material characteristics to be allocated to products produced in the form of “credits”, even if this does not align with the actual sourcing composition of the product.
How does mass balance characteristic allocation work?
Where the mass balance approach gets complex is its ability to allocate various amounts of a characteristic (e.g. sustainable material) to the products produced in a process, regardless of its actual chemical composition.
If a process has inputs of 50% sustainable and 50% virgin material, then the products produced will all be made from a 50-50 split of materials. But mass balance allows materials to be virtually allocated to some of the products as long as the overall proportion of input characteristics is reflected in the output.
This means that a larger proportion of the sustainable material can be virtually allocated to some of the output products in the form of credits, so half of the products could be sold as “contributing to sustainable materials”, but the other half of the products must then be sold as “not contributing to sustainable materials”, in order to maintain the balance of the system.
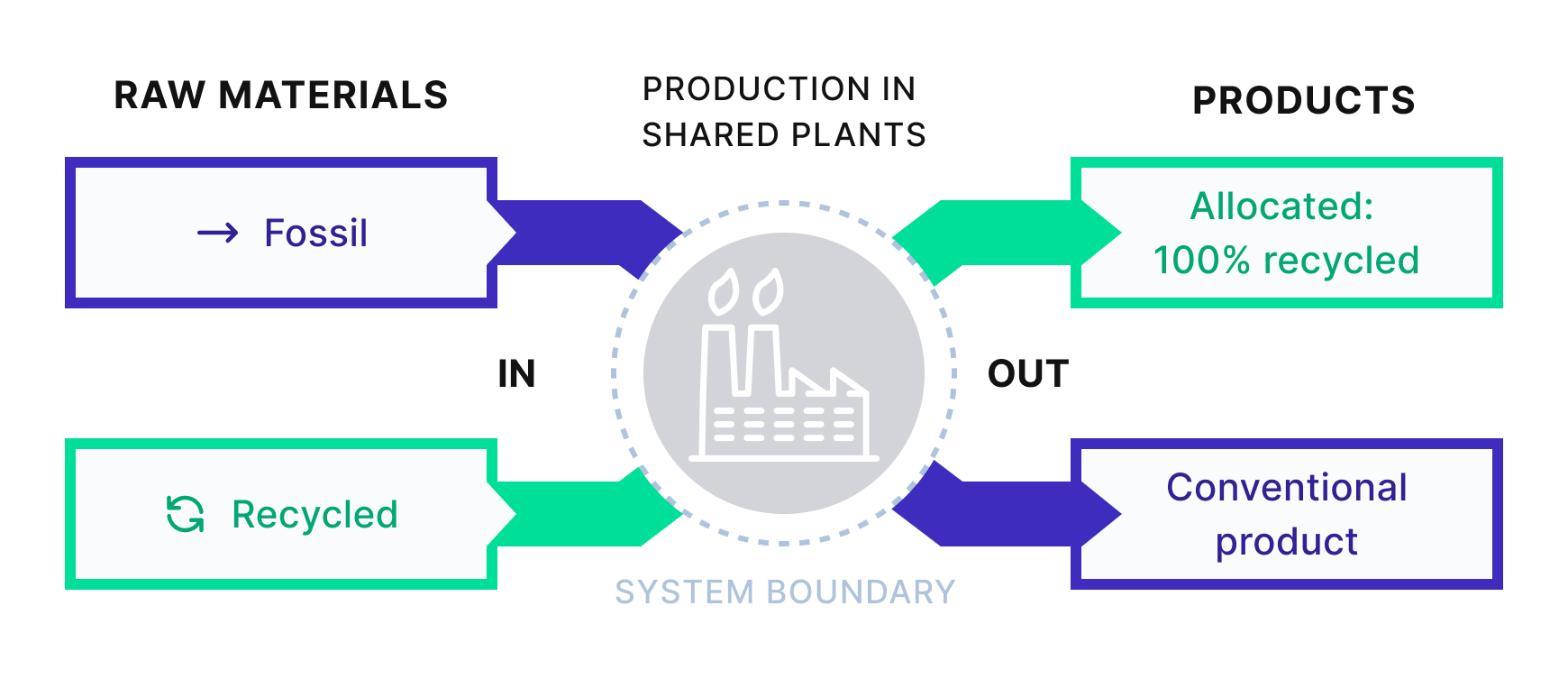
What happens in between is less relevant, as long as the ratio of recycled and fossil material inputs matches the output, considering a few boundary conditions in the calculation. We are following the boundary conditions defined by the Ellen MacArthur Foundation5:
- First, the conversion factor for each process needs to be set to determine how many tons of feedstock are required to produce one ton of output.
- Second, the proportion of recycled to fossil stock is calculated.
- Third, the system boundaries in space and time must be determined, i.e. the set of production assets, plus the time period during which the recycled feedstock is booked in and when the recycled content of the products is booked out must match.
Products made from mass balanced material are then booked with claims such as: “1 ton of recycled polyethylene is used within the system boundary” or “the value analysis of 1 ton of polyethylene shows the feedstock requirement meets 80GJ, from a recycled feedstock (55GJ/tonne) required for 2 tons of recycled feedstock within the system boundary for a 100% recycled claim.”
How does mass balance work across sites and organisations?
Credits for material characteristics, such as post-consumer recycled and bio-based plastics, can also be traded between nearby sites within an organisation. This allows certified sustainable materials to be shipped from any production facility, in order to prevent longer transport routes, if the nearest facility to a customer does not have the required product in stock. Transfers can be within production sites, or within a group of companies, even between neighbouring countries.
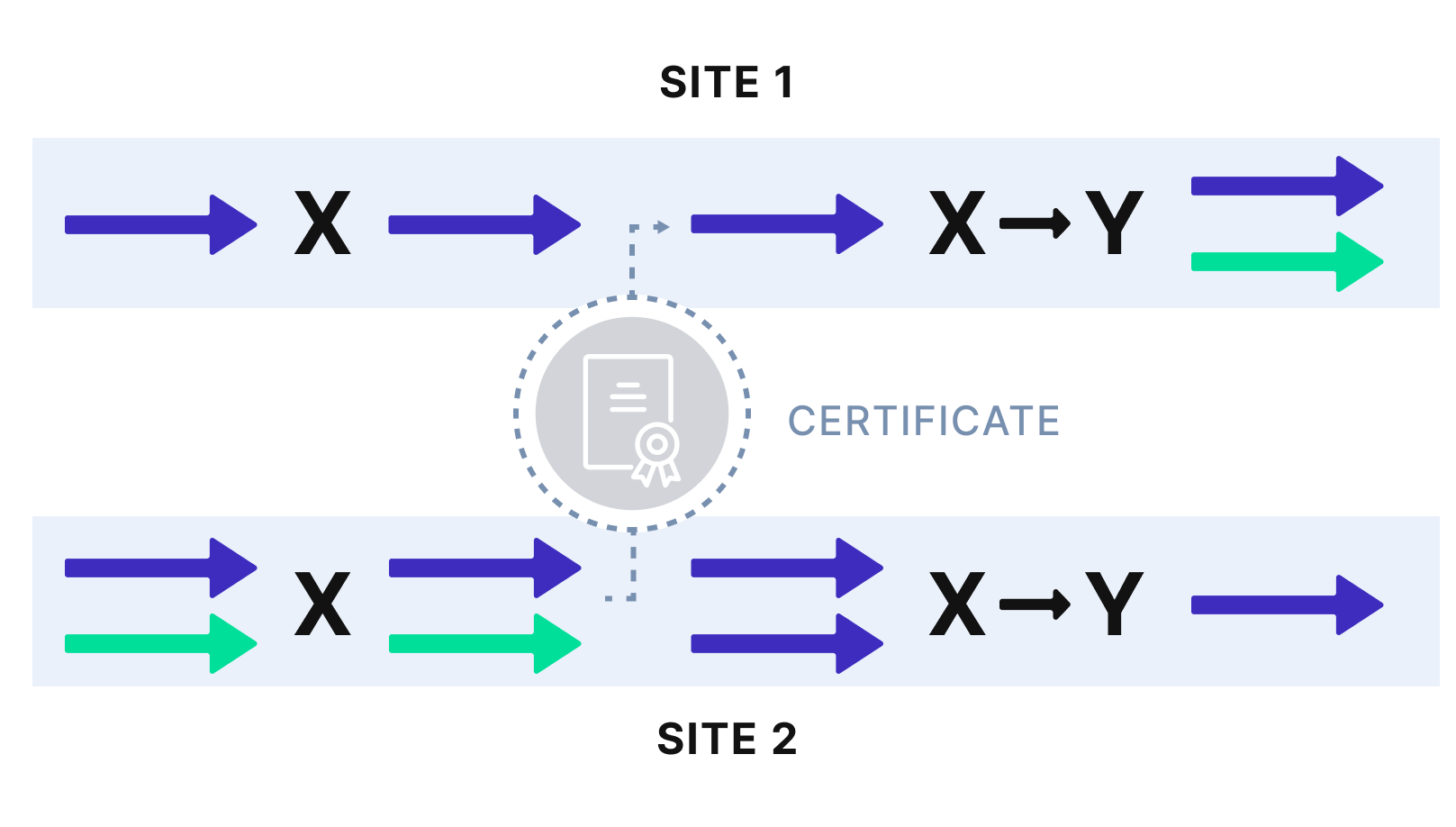
While some people may see this as misleading, the mass balance approach ensures that overall no sustainable material is oversold (over-allocated). This allows for industrial processes to incrementally increase the proportion of sustainable material feedstock over time and therefore the proportion of products made from sustainable materials. The key is to consider the net inputs and outputs of the process.
How can mass balance material allocation be guaranteed?
There are a variety of mass balance certification schemes which aim to ensure that the approach is fairly upheld. While they use different frameworks, they require a similar structure for documenting and reporting the mass of all material inputs and outputs.
- You need a system for documentation and reporting. In order to ensure the mass balance approach is being used correctly, a strict documentation and reporting system must be maintained in order to preserve trust in this method. According to ISO 22095:2020, a bookkeeping system must be used to track the inputs and outputs of all the materials flowing through a process to which the mass balance approach is being applied (excluding energy sources).
- An independent third party must do an audit. Once the internal auditing process is established, the bookkeeping system, materials used, and reporting system must be certified by an independent third party (certification body) to ensure the integrity of the material allocation process.6
- You will report periodically. The overall balance must then be reported periodically to ensure continuous compliance that the output credits do not exceed the input credits for that bookkeeping period.
- You can trade materials accompanied by sustainability declarations. Credits for sustainable materials can then be allocated to an output material, as long as the net proportions of material characteristics are preserved. When materials are traded between companies they must be accompanied by a certificate for that material (a sustainability declaration), corresponding to its sourcing and a declaration of its sustainability profile.
While various third-party certification schemes follow the general principles of mass balance, each scheme has slightly different frameworks and focus, which we outline in the next section.
Mass balance schemes and examples
Mass balance certification schemes
Certification schemes for mass balancing vary based on their method of accounting for the balance of material, energy, and carbon use. These differences relate to targeting specific industry segments or governance requirements for sustainability criteria reporting.
Better Biomass (previously NEN)
The Better Biomass certificate is used to demonstrate the sustainable production of biomass and is an approved method to demonstrate compliance with the biomass production requirements of REDII and the Dutch Decree for biomass conformity assessment.7
Ecoloop
This certification scheme is tailored for tracking chemical and recycled plastic feedstocks across plastic producers, recyclers, processors, and manufacturers of plastic products.8
EU Standards: Material Balance Standard for Bio-Based Products
This is a standardised method of determining the proportion of bio-based content in materials which has been approved by the European and Swedish parliaments (SS-EN 16785-2:2018).9
EUCertPlast
The EUCertPlast scheme is developed in accordance with European Standard EN 15343:2007 with the European Commission to guide plastic recyclers to ensure compliance with REACH food contact requirements through traceability.10
ISCC PLUS
International Sustainability and Carbon Certification (ISCC) PLUS is a certification scheme for sectors outside of the EU renewable energy or fuel quality directives, such as foods, chemicals and plastics. The ISCC System is centred on a multi-stakeholder approach where all members of the supply chain wishing to take market products with the ISCC certification must have some degree of ISCC certification.11
In terms of overall mapping, the ISCC PLUS is a stricter approach and requires cross-supply chain cooperation, but it can be applied to most use cases in bio feedstock, chemicals and fuel industries. By comparison, the REDcert2 and RSB Advanced Products schemes allow for greater flexibility in the overall mapping but take specific focuses within particular industries.
REDcert2
The REDcert2 scheme focuses on certifying the flow of sustainable materials within the chemical industry and carries more restrictive rules relating to the transfer of material characteristic credits. It is based upon a scheme developed by BASF SE and TÜVSÜD in 2012.12
RSB Advanced Products
Roundtable of Sustainable Biomaterials (RSB) Standard for Advanced Products focuses on segregated material flow for bio-based and recycled material-based products, and mass balanced products produced in combination with fossil feedstock. RSB AP is stricter in relation to the need for physically existing process steps.13
RSPO
The Roundtable on Sustainable Palm Oil (RSPO) aims to ensure the production of palm oil is done in a sustainable manner and supports the four main chain of custody models including mass balance in its certifications.14
UL 2809 Recycled Content Standard
ULs environmental claim validation procedure is used to evaluate the amount of post-consumer, pre-consumer, closed-loop, and total recycled content of products. UL is a popular option in North America, acting as both a certification scheme and body. They are also known for having stricter standards, and conducting chemical analyses of products to ensure claims about material input proportions are correct.15
Mass balance reporting example
Here is a fictional example of the information required for brands and retailers which sell products made with ISCC certified material and wish to use this claim publicly. Bookkeeping on all incoming and outgoing material must be maintained for brands to have an ISCC licence.16
Incoming material:
- ISCC PLUS sustainability declaration number: 000 123 456
- Name of supplier: Plastic Supply
- Total amount of ISCC certified material in metric tons: 50’000
- Total amount of ISCC certified material in number of pieces: 1’000’000
- Product name as in licence agreement: Polyethylene
- Raw material category: Biobased plastic
- Percentage of certified material: 80% certified plastic
Outgoing material:
- Total amount of ISCC certified material in metric tons: 40’000
- Total amount of ISCC certified material in number of pieces: 800’000
- Product name as in licence agreement: Toy Rocket
- Product type and description: Plastic toy
- Raw material category: Biobased plastic
- Use of on-product logo: No
- Use of on-product claim: Yes
This is the information required for ISCC licence holders, a minimal scheme for brands receiving materials from suppliers which are ISCC EU and ISCC PLUS certified. The certifications for the material providers and processors require far more extensive bookkeeping on the mass balance approach.
Challenges and benefits of the mass balance approach
Challenges of setting up a mass balance system
Level of knowledge and awareness
One of the greatest challenges the mass balance approach faces is awareness. It is not a well-understood concept even throughout the plastics and chemicals industry. The detachment of physical product movement from reported numbers leads to confusion and when not fully understood, distrust. Ultimately if a customer cannot be convinced of the value of using this approach, then there is little incentive for a company to use a mass balance method for more product lines and increase recycled feedstock content.
Resourcing the certification process
Preparing all the information required for mass balancing and getting internal processes set up is a significant project. This can be a considerable resource drain on a small to medium enterprise. For larger companies, coordinating certification efforts across many sites and departments is a huge undertaking.
If an effective management system is not set up, it can also lead to a substantial ongoing administrative burden which could also invite errors in ensuring balanced bookkeeping.
Bookkeeping administration is manual and complex
Setting up an efficient way of managing material credits, physical material, and financials in a non-manual way is difficult and likely expensive. The difficulty comes when building a management system to cope with a complex production system with many inputs and outputs and processes which are spread across multiple facilities. Transferring credits to other regions within the same company also creates added complexity.
Without an effective planning and booking system, issues like premature allocation or double counting can cause non-conformity in records. That can, in turn, lead to losing your certificate and even worse, losing the trust of your customers. An ineffective system also then hinders scaling the process to more product lines. The barrier to entry is compounded when companies across whole supply chains have to undergo this process in order for the sustainability claims to be preserved.
Strict certification also limits sustainable material adoption
While ensuring all companies in a supply chain are certified to trade mass balance material and certificates helps protect the reliability of the scheme, it also hinders the adoption of such a scheme. If sustainability claims relating to the material can only be made by certified companies, it means that it is only really valuable for certified suppliers to sell to certified buyers, greatly limiting the market for sustainable material.
As different types of companies require different certifications based on their operations, and with several certification schemes available, it can be difficult for a buyer to establish if the material they are buying is adequately certified and if they have the ability to actually take advantage of the sustainable characteristics of the material they are purchasing.
The double counting problem
Certification systems currently rely on pdfs and paper as a medium for maintaining an audit trail. Unfortunately, this means that either intentionally or accidentally, credits can be allocated multiple times by editing the quantity or percentage of sustainable material in a product. As audits are typically only once per year, it means that all records cannot be reviewed and if a mistake is found, it is too late as the product has already been sold. This is the challenge when implementing a tracking system which requires data input from many different private sources and must then be shared reliably.
Add-ons and data gathering
Some certifications allow for additional criteria to be tracked beyond just recycled or bio-based content of materials, such as GHG emissions. However, similar to life cycle assessments (LCAs), there is currently no single, clear standard for these audits, compromising the validity and comparability of the data gathered.
Even if a clear standard for gathering GHG emissions is established, conducting this audit requires a lot of time and effort, especially if trying to account for scope 3 emissions as suppliers are rarely willing to be totally transparent about their operations in order to get an accurate measure.
Although actors throughout the supply chain need to be certified with a mass balance certification scheme, the information downstream businesses receive in sustainability declarations and credits is minimal. Companies have to place trust in the auditing processes of certified bodies and the integrity of their suppliers.
Lack of audits at the beginning of the supply chain
The first collection point of material in a mass balance system aiming to demonstrate bio-based or sustainable sourcing, often comes in the form of biomass from sites like farms. In order to meet the demand for sustainable feedstock, there must be input from many sources, often in relatively small quantities. Due to the sheer number of facilities providing feedstock, it is currently not possible to audit them all, therefore these sites do not have to undergo the same extensive certification process as the other members of the supply chain.
While more relaxed requirements for material inputs facilitate greater adoption of sustainable feedstocks, it also creates a weak link in the system. Without such strict requirements, it means that it is easier to input fraudulent material into the system, as it is not closely monitored. This risks leading to the concept of “garbage in, garbage out”.
Methods of determining credits allocated to materials
There are different ways of determining credits allocated to materials in the mass balance approach, i.e. determination based on mass, energy, tracing the atom or isotope, etc. A similar product must be used in a physical process in order to produce a certified material - a credit cannot be processed without the movement of actual material. However, there are different methodologies in determining input to output credits.
When producing a certified product, certified feedstock must be used, but mass determination (using exact credits according to a product’s recipe) is not always used. If a process requires three different certified inputs (x, y, and z) to create a certified product (xyz), most companies will mirror the physical transformation with the credit transformation e.g. x + y + z =xyz. But technically this is not required in order to maintain the mass balance approach.
Say a company doesn’t have credits for y or z but they want to sell certified xyz, they could use more x credits to produce xyz credits, and use another determination model, such as energetic, to create product xyz. This means that in reality, they can use uncertified y and z to make certified xyz, and on the bookkeeping system they can record 3x = xyz, even if this is not possible in reality. Depending on the product, there are companies that will ensure that the balance of carbon atoms or the balance of potential energy of inputs and outputs is the same on the books, while they continue to use many uncertified inputs to make a certified output.
The benefits of mass balance
Using the mass balance chain of custody approach allows many industries to begin the gradual switch to more sustainable practices and material usage. This is key when making a significant operational change in one step is not possible and setting up segregated processes for using sustainable and virgin materials is not practical.
Driving the system-wide transition to a circular economy
“Circularity is fundamentally a collective action. If we can encourage more companies to use more sustainable materials, we are closer to our common circularity goal. For tools like mass balance, it is not a solution to circularity; it is one of the enablers.”
- Natalia Scherbakoff, Trinseo’s Global Technology & Innovation Director. 17
Facilitates progress through incremental change
“The advantage of mass balancing is that it enables the industry to have an immediate impact in combating climate change. More sustainable solutions can be introduced incrementally… Mass balancing thereby accelerates the reduction of GHG emissions.”
- Isabella Tonaco, Vice President of Strategy Execution & Marketing at Neste.
Transitioning to meet recycled content and net-zero targets
“Here at Borealis, we see mass balance as an effective way of increasing both the recycled and renewable content of our products, leading to a reduced climate and environmental footprint over their lifecycle. It’s also how we support the uptake of recycled plastic waste and renewable feedstock in new products, and is currently the only way to effectively meet the EU’s recycling and future recycled-content targets.”
- Eugenio Longo Head of Sustainability & EU Affairs, Borealis. 18
Setting up a mass balance reporting mechanism also allows for live tracking of improvement of GHG (greenhouse gas) footprint of product portfolio being traced. This data collection allows for tracking progress to net zero and circularity targets and provides certified numbers on sustainability metrics for company corporate sustainability reporting (CSR) and marketing. When a mass balance scheme requires cross-supply chain cooperation such as ISCC PLUS, it also provides confidence that environmental reporting information from tier 2 and tier 3 suppliers is reliable.
Allowing consumers and businesses to make informed buying decisions
Mass balance certifications help to convince consumers that claims are substantiated.
Supply chain-wide tracking can provide visibility to the end customer with validated sustainability criteria, helping avoid actors across the supply chain to avoid making wrong claims. In turn, this helps companies to decrease the risk of unintended greenwashing.
Efficient information sharing
“In an ideal world where mass balance reporting is fully integrated with internal IT systems, the sustainability declaration and audit process can be almost entirely automated, increasing efficiency significantly by having a single digital repository. However, setting up such a system manually is a significant undertaking due to all of the custom integration of systems required.”
- Mesbah Sabur, Co-founder of Circularise.
Conclusion
Mass balance acts as a practical path for industries like chemicals and plastics to transition to sustainability in a continuous manner. However, there are many considerations to be taken when deciding how exactly to adopt the mass balance approach.
Setting up the auditing process and bookkeeping system can make or break this initiative within companies. When done effectively it can generate more value for the business and act as a means of sustainable transformation. But when not properly set up it can create a large continuous administrative burden which leads to confusion and resentment internally and externally, thus mitigating the new value creation that can be obtained from providing products with verifiable sustainability claims.
Where to start with implementing a mass balance approach?
- Firstly you need to be sure mass balance is the chain of custody model that is best for your market and your business operations.
- Next select a certification scheme that best suits your business, considering the benefits, market demand, scalability, and standards that will need to be met.
- Outline a plan or MVP for a system which will allow your company to maintain reliable bookkeeping for the certification you have selected.
- Find a certification body that will conduct the auditing for the certification for your site(s) and product(s).
- Outline a practical timeline for implementation, considering the operational change and auditing steps required.
Circularise is the leading software platform that provides end-to-end traceability for complex industrial supply chains. We offer two traceability solutions: MassBalancer to automate mass balance bookkeeping and Digital Product Passports for end-to-end batch traceability.